REVERSE
ENGINEERING
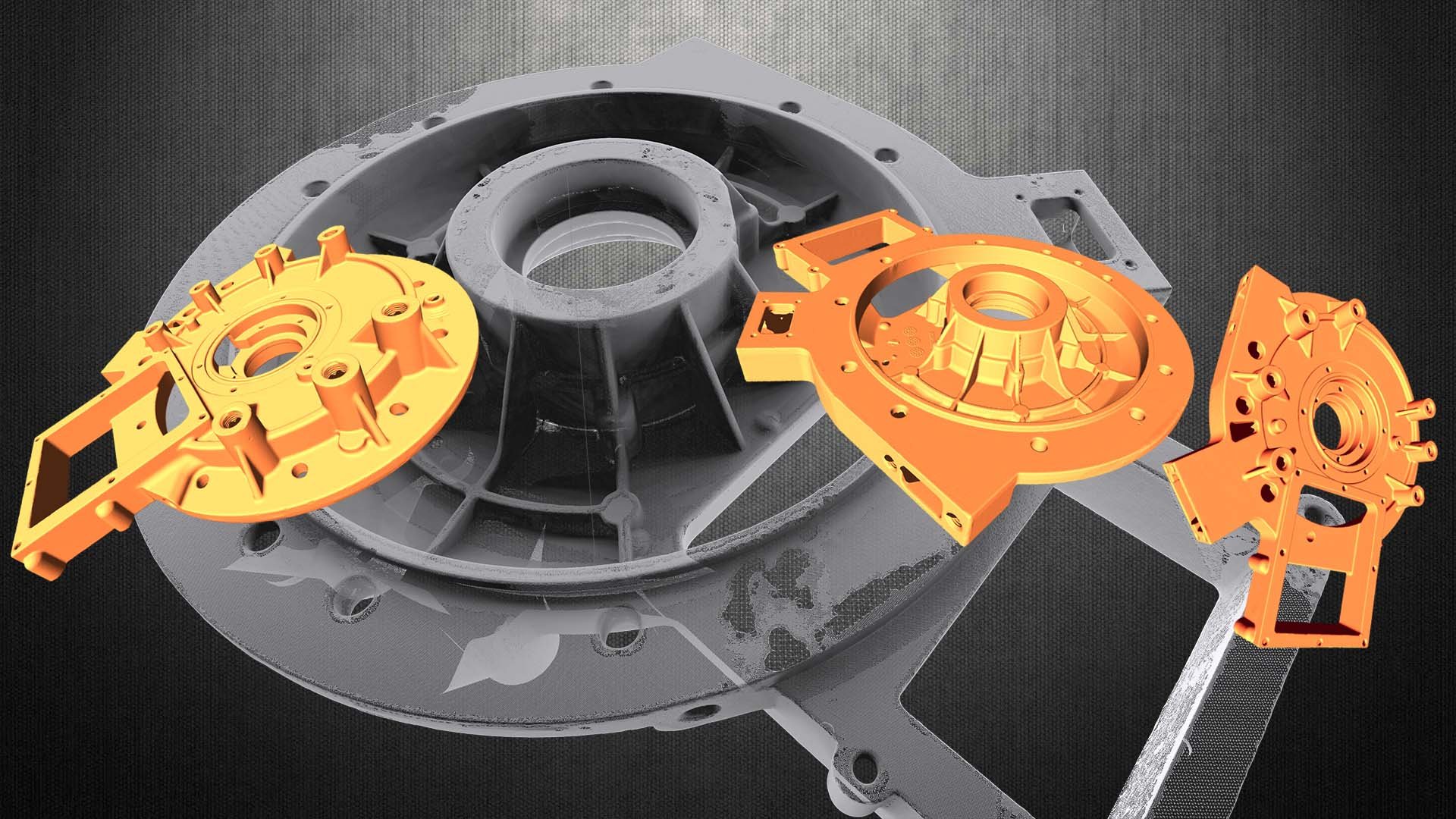
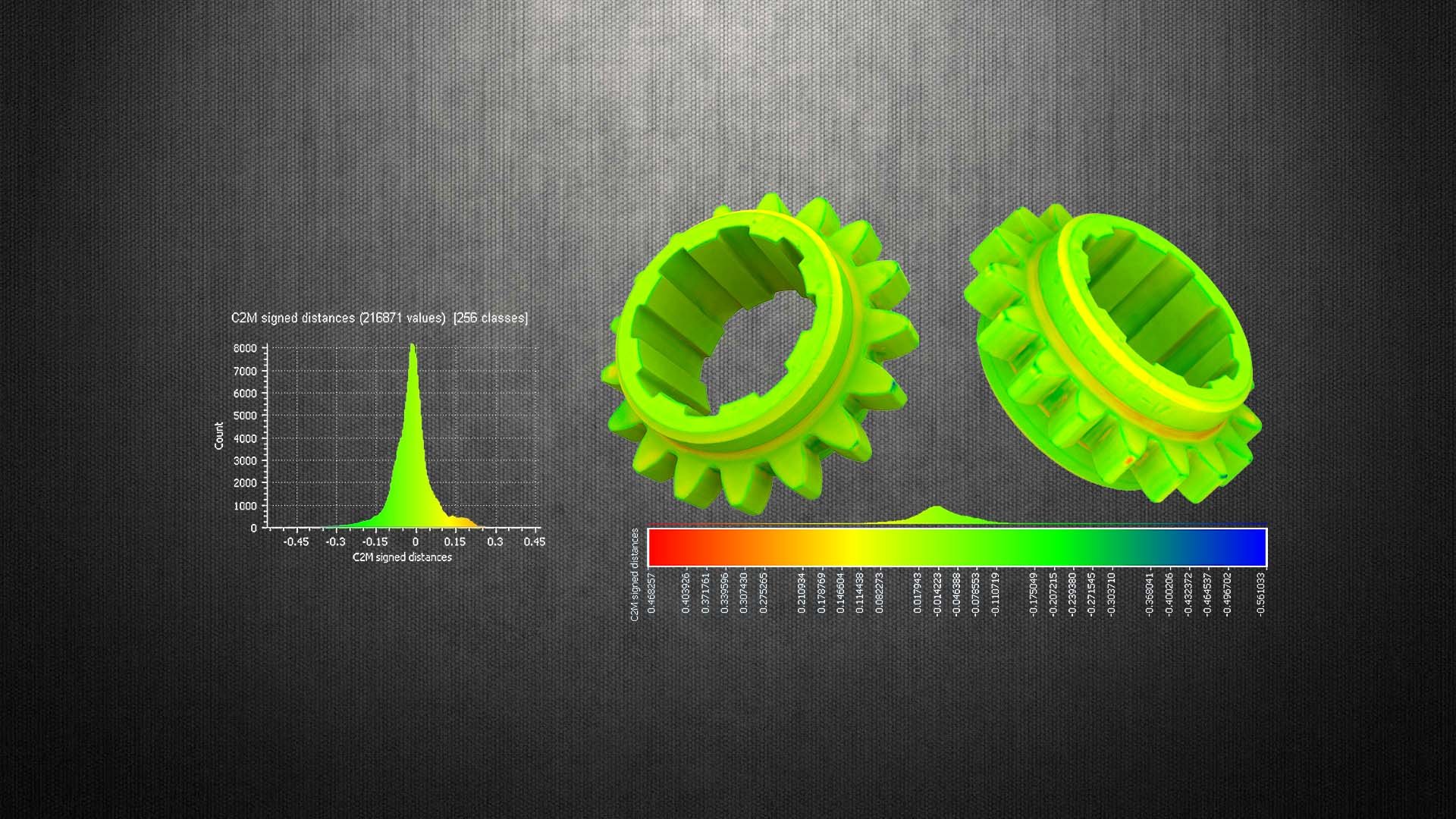
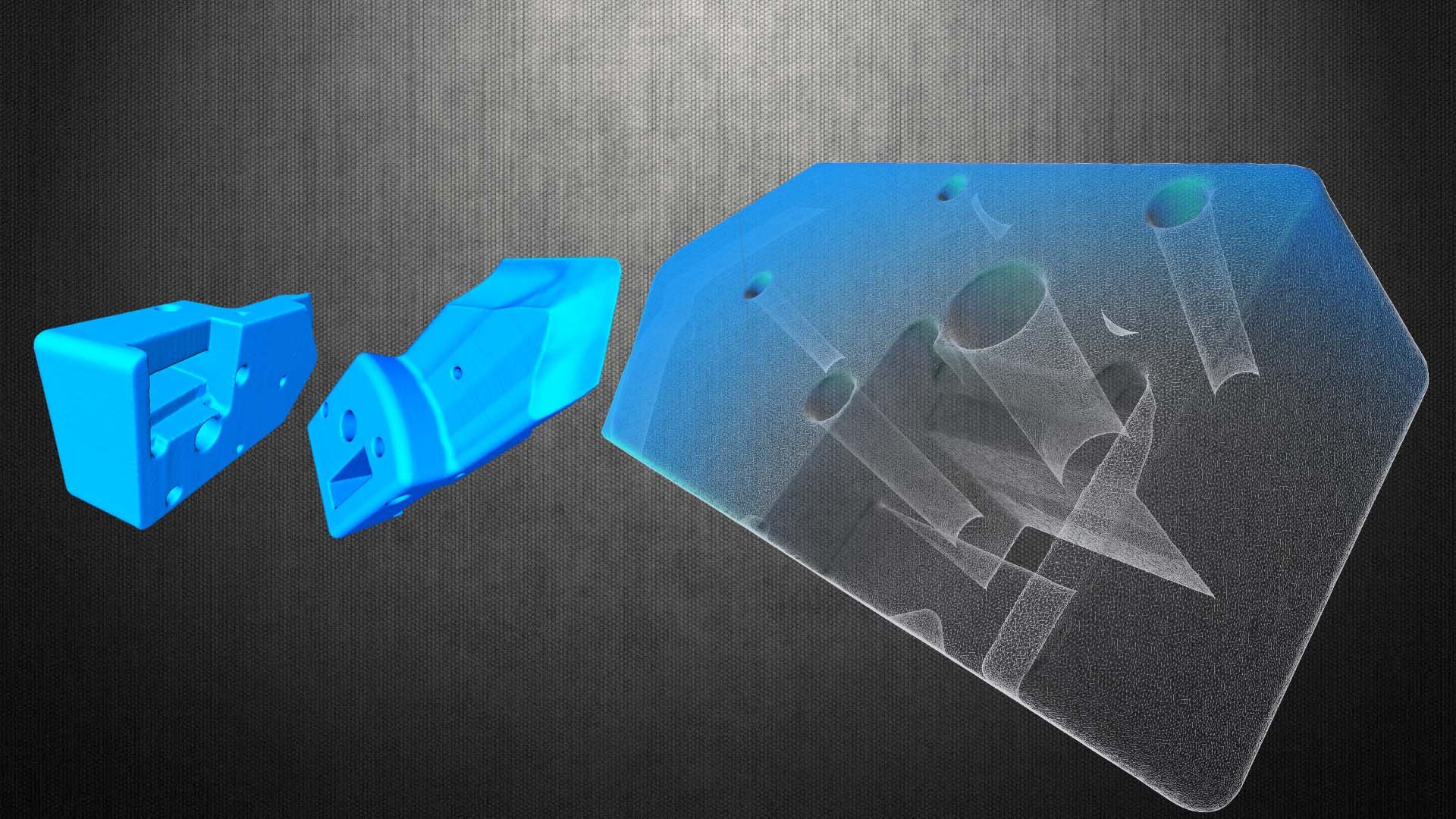
REVERSE ENGINEERING
Reverse engineering through 3D laser scanning and coordinate measuring machine (CMM) measurement is the most efficient and effective method for creating accurate digital conversions of objects. In reverse engineering, a 3D model is generated from a point cloud or a 3D mesh model, which is obtained through 3D laser scanning, CMM measurements, or both. This process is widely used across industries to create 3D models of specialized parts and equipment, for example, to enable CNC milling or 3D printing. It is also commonly employed to produce digital twins, 2D CAD technical documentation, and assist in the development and modification of equipment, speeding up processes and reducing costs.
To reverse engineer small to medium-sized objects, we often employ a combination of CMM measurements using our measuring arm and laser tracker to achieve the greatest measurement accuracy and metrology-grade handheld 3D laser scanning to capture the smallest features. For medium to large-sized objects, we commonly use a combination of our laser tracker and terrestrial 3D laser scanner for the greatest level of accuracy and detail. Additionally, we frequently perform X-ray Fluorescence (XRF) analysis to accurately determine the material composition, such as the specific type of stainless steel, ensuring the reverse-engineered part is completely identical to the original.
Specialized software and workflows allow us to convert the raw data obtained from our CMMs and 3D laser scanners into accurate as-built 3D CAD models, which can then be further converted into as-built 2D CAD models and drawings. Additionally, by comparing the raw data obtained from our CMMs and 3D laser scanners with as-built 3D CAD models or existing models, we can generate deformation color maps for further inspection and analysis.
AS-BUILT SERVICES
Registered Point Clouds
3D Mesh Models (Scan to Mesh)
2D & 3D CAD Models (Scan to CAD)
Machinery Alignment & Inspection
Deformation & Wear Analysis
XRF & Thickness Analysis
APPLICATIONS
Creation & Inspection of Specialized Parts & Equipment
Digital Twin
Industry & Energy
Marine & Offshore
Aerospace
PRODUCTS
SCAN TO CAD


POINT CLOUD
CAD MODEL